The Nanoscale Imaging and Surface Analysis Lab has a sample preparation room that houses equipment for mechanical cutting and polishing and ion mill for final surface polishing. The dual beam Helios 650 FIB can also be used for micrometer scale sectioning and TEM sample liftout.
DUAL BEAM SEM/FIB: HELIOS NANOLAB 650
- High-resolution imaging <10 nm resolution for conductive materials
- Elemental contrast using backscatter electron imaging
- Low-voltage, low-current imaging of non-conductive samples
- Elemental mapping and semi-quantitative compositional analysis using energy dispersive spectroscopy (EDS)
- Automated particle morphology and elemental analysis using EDS
- Grain analysis (grain size, orientation and texture) using electron backscatter diffraction (EBSD)
- Sectioning of thin specimen using ion beam
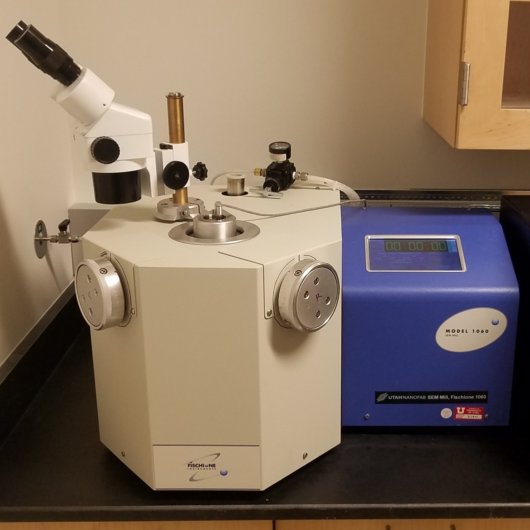
FISCHIONE SEM MILL MODEL 1060
- Two independently adjustable TrueFocus ion sources
- High energy operation for rapid milling
- Low energy operation for sample polishing
- Adjustable beam diameters
- Individual, automatic ion source gas control
- Fully integrated dry vacuum system
- Continuously adjustable milling angle range of 0 to +10˚
- Sample rocking or rotation
- Stereo microscope for direct sample observation
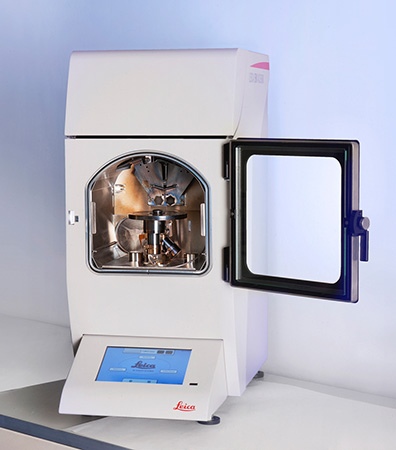
LEICA EM ACE600 SPUTTER COATER
- enhance contrast by a fine-grained metal layer
- produce nanometer thin but robust carbon films
- rotary shadow your sample to make smallest features visible
- different coating methods sputtering, carbon thread, carbon rod and e-beam evaporation with up to two methods can be used at the same time in the same instrument
- angled sources attached to a metal vacuum chamber and a rotating stage to allow evenly distributed films on a stage size over 100mm
- fully automated coating process ensures that the conditions are the same for each run
- quartz crystal thickness measurement in the middle of the stage, gives full control over the result
- coated layer can be set to a low 10-6mbar (even less is possible) value for high resolution imaging or to the 10-4mbar range
- ultrathin, robust and stable Carbon coating system using adaptive pulsed carbon thread method
- low angle coating technique to create visible shadow on the sample using the angled e-beam source together with a motorized 3-axis movable stage
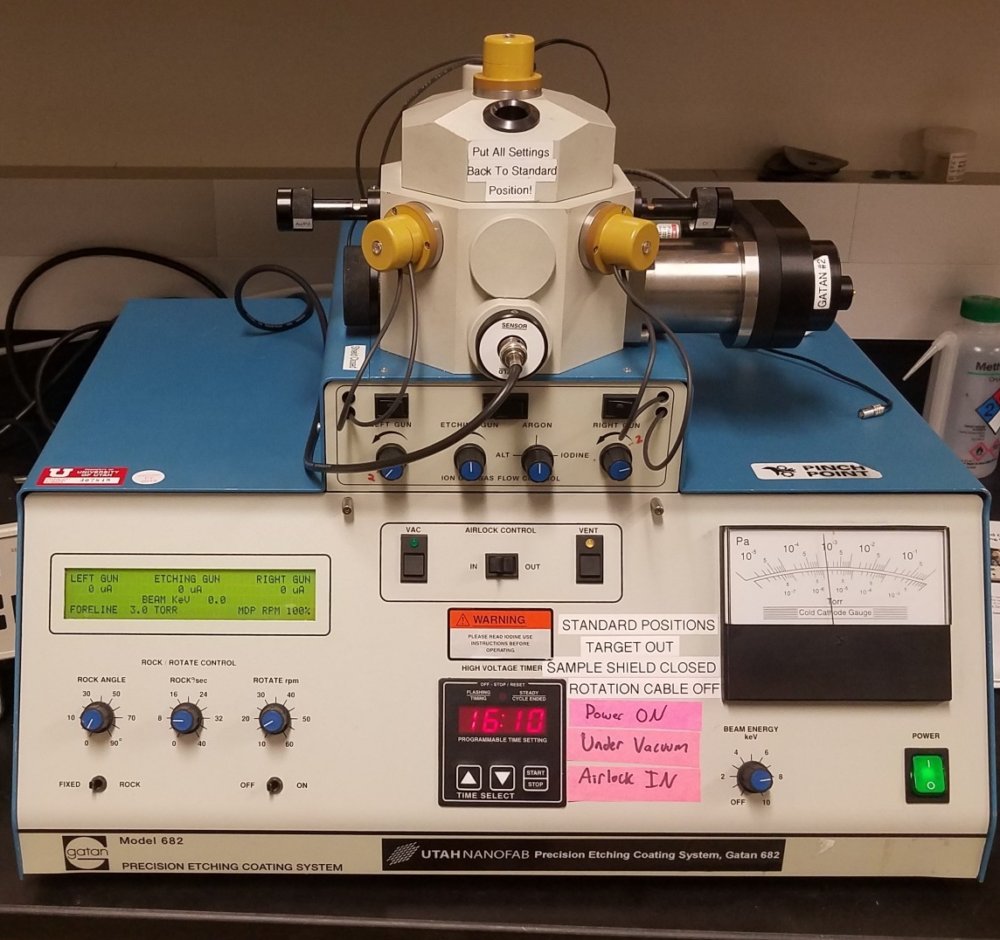
PRECISION ETCHING CATING SYSTEM (PECS)
- Fully automated argon ion polishing system suitable for preparation of SEM samples to prepare damage free surfaces, cross sections and deposit coatings to prevent or eliminate charging
- Polish, etch or coat samples with a single pump down
- Etch at voltages as low as 100 V for rapid and damage free preparation of sample surfaces
- Permit samples as large as 32 mm in diameter
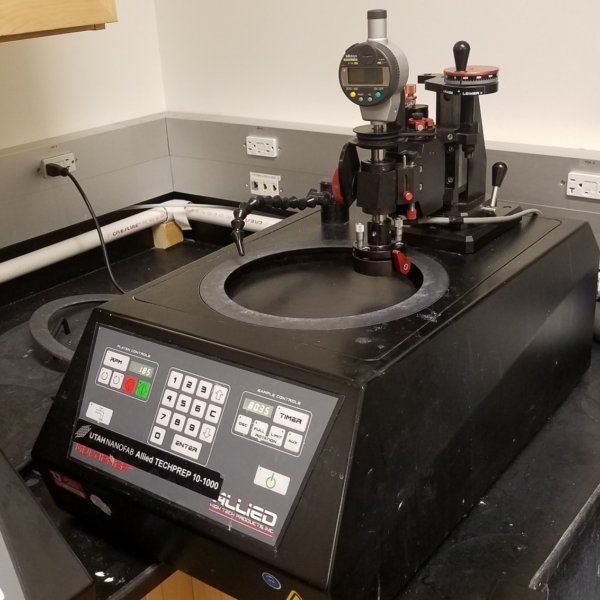
ALLIED MULTIPREP POLISHING SYSTEM
- Precision spindle design indexes the sample perpendicular to the platen, and can rotate simultaneously
- Front digital indicator displays real-time material removal (sample advancement), 1 μm resolution
- Dual Axis, micrometer controlled angular positioning of the sample (pitch and roll), +10/-2.5° range, 0.02° increments
- Rear digital indicator displays vertical positioning (static) with zeroing function, 1μm resolution
- Automatic sample oscillation, adjustable sweep with 6 speeds
- Full or limited automatic sample rotation with 8 speeds
- Cam-locking system eliminates the need for tools and allows for precise repositioning of fixtures
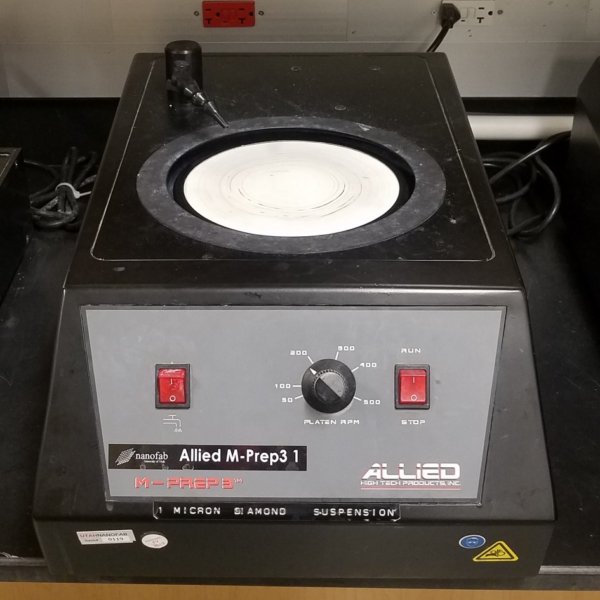
ALLIED M-PREP 3 GRINDER/POLISHER
- Variable platen speed: 5-350 RPM, in 5 RPM increments
- Touchpad switches control all functions
- 0.5 HP (375 W), high-torque motor
- Stable RIM, aluminum and stainless steel construction
- Digital timer and tachometer
- Electronic coolant control with adjustable valve
- Clockwise/counterclockwise platen rotation
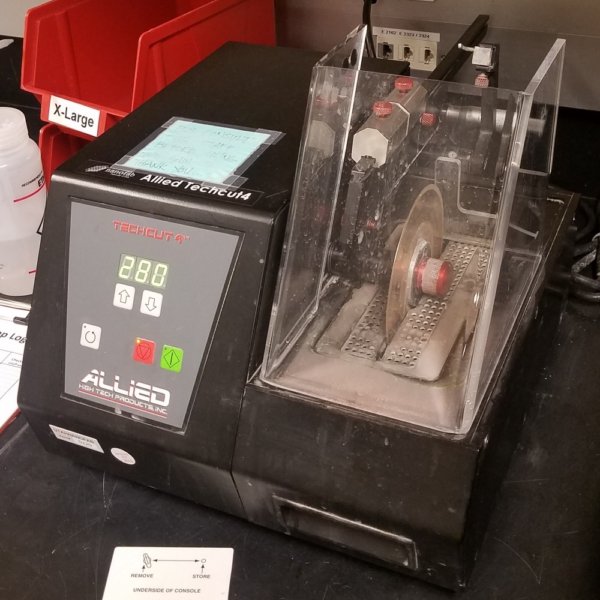
ALLIED TECHCUT 4 PRECISION LOW SPEED DISC SAW
- Gravity-fed cutting system
- Variable speed with LED display: 10-500 RPM (10 RPM increments)
- Cutting capacity: 2" (51 mm) thickness
- Micrometer sample indexing, 2 µm resolution, 1.5" (38 mm) range
- Spring-retractable dressing stick attachment for dressing while sectioning
- Optical shut-off sensor with adjustable stop to control depth of cut
- Sliding weights that provide variable sample loading: 0-300 grams
- Touchpad switches to control all functions
- Removable splash shield
- Removable coolant reservoir
- Removable catch screen that prevents sectioned pieces from falling into reservoir
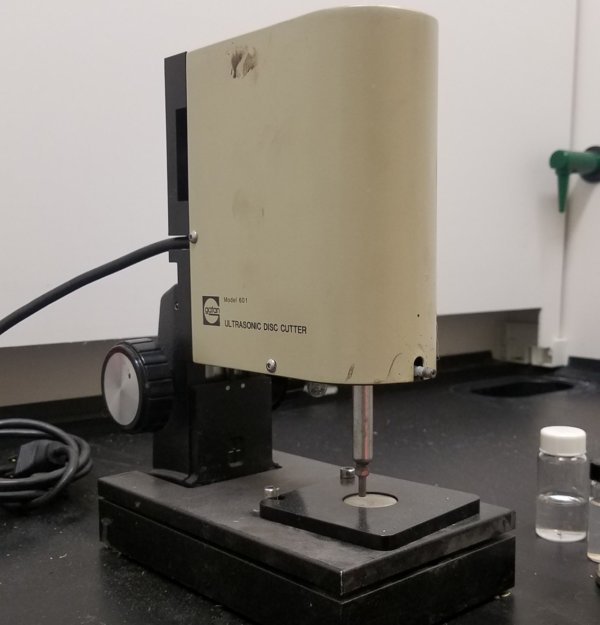
GATAN ULTRASONIC DISC CUTTER
- Cut 3 mm discs from hard, brittle materials such as semiconductors, ceramics and geological materials
- Material thickness can range from <40 μm to 5 mm utilizing a piezo-electric crystal driving a tubular cutting tool in a fine grain, boron carbide slurry
- Minimize mechanical and thermal damage using manually tuned frequency driver to optimize cutting speed
- Reduce edge chipping and sample damage with spring-loaded platforms and magnetically held table to prevent lateral movement
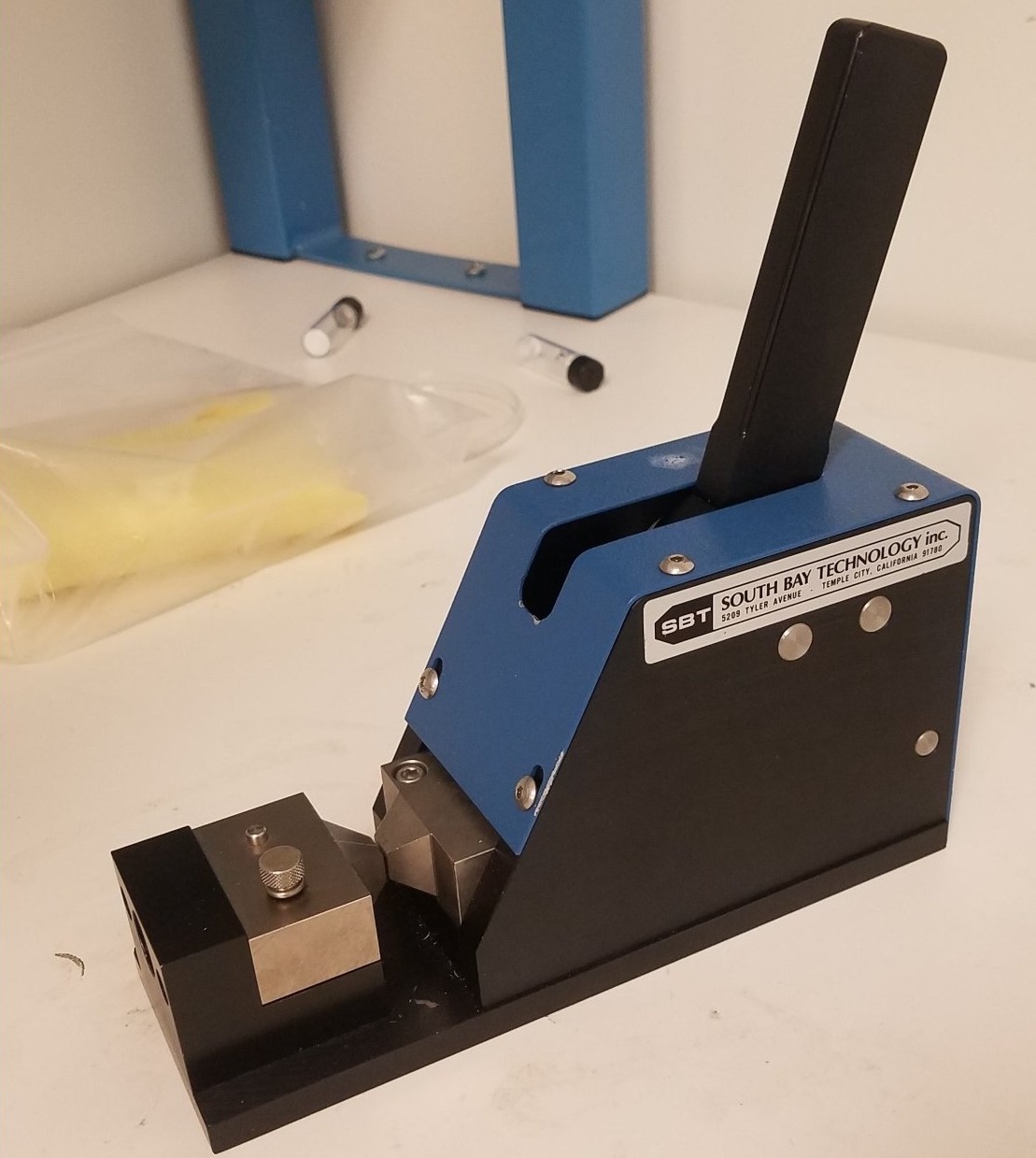
DISC PUNCH SYSTEM
- Punches 3-mm discs from malleable materials. Useful for metals
- Produces sharp cut edge
- Allows fat, single motion multiple punching
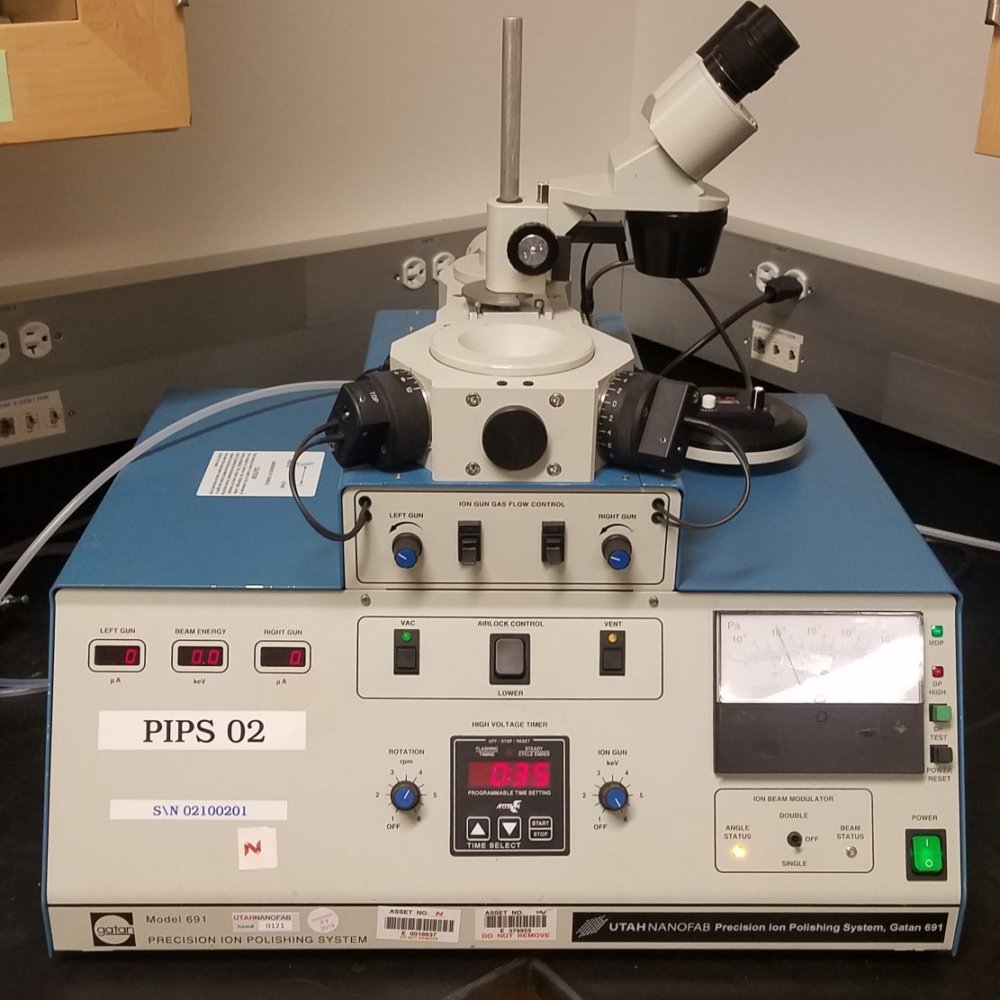
PRECISION ION POLISHING SYSTEM (PIPS)
- Used for precise centering, control and reproducibility of ion milling process
- Can etch dimpled samples up to a few tens of nanometer in thickness for TEM imaging
- Minimize mechanical and thermal damage using manually tuned frequency driver to optimize cutting speed
- Etching can be done at angles between 1 - 10° with respect to sample surface
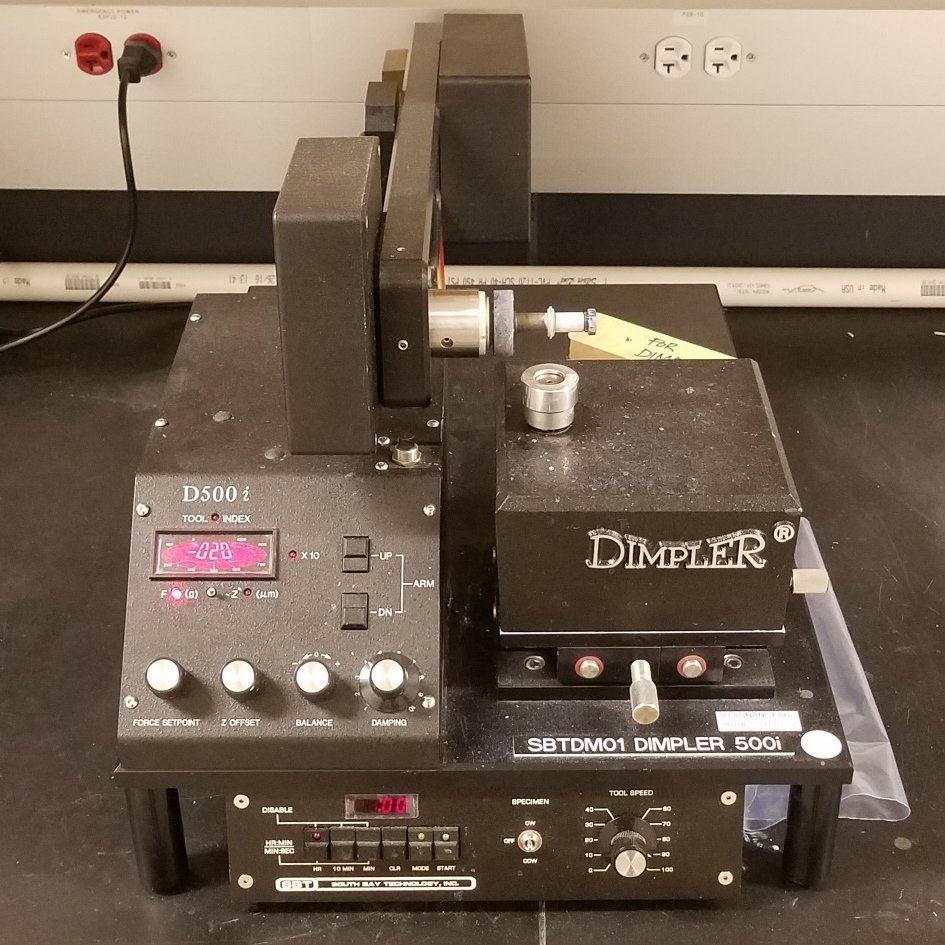
DIMPLE GRINDER
- Used for pre-thinning of materials to near electron transparency to reduce ion milling times and uneven thinning
- Utilizes large thin and flat wheels to preserve large transparent area after processing
- Leaves a thick supporting rim to protect specimen after dimpling
- Produces final thickness <10 μm in dimpled specimen
- User defined stop point and real-time display for accurate depth and thickness control
- Provides both orthogonal and intersect axes for more accurate sample positioning